Methods of costing helps to determine the cost of the final product, various methods and techniques have been developed for cost accounting to meet the specific needs of the business organizations.
The methods for calculating cost of production differ from industry to industry, it varies according to the company’s requirements. The methods of analysis and presenting the costs are different for different industries because of the difference in the nature and type of products produced or services rendered.
Table of Contents of Methods of Costing
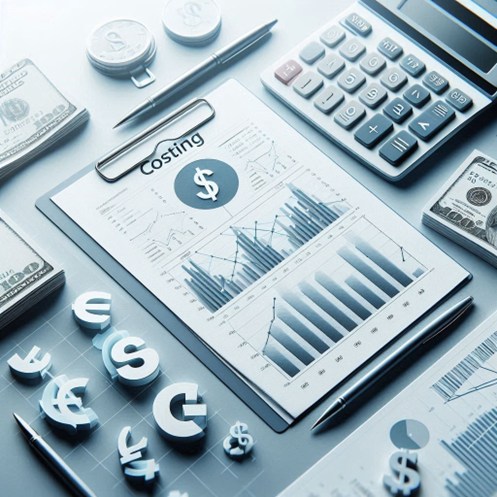
What is Costing?
Costing is figuring out how much it costs to make a product or provide a service. It includes adding up expenses like materials, labor, and other overheads. By understanding these costs, businesses can set the right prices, manage their budgets, and ensure that they make a profit.
Basically, there are two Methods of costing that are:
(i) Specific Order Costing
(ii) Operation Costing
(i) Specific Order Costing:
These Costing methods are applied where the work or job is of a special nature (i.e. according to the special requirement of the customer). As the design of a dress, design of furniture, design of the house etc. Under this Costing method production takes place only when the order is received from the customer.
These Costing include:
(a) Job Costing
(b) Batch Costing
(c) Contract Costing
(a) Job Costing:
Jobs Costing are to be performed under the specific instructions of the individual customer. Every customer has special taste, design, quality of work and spending power. Costs are determined for each job or work order separately. The job may consist of a single unit or it may consist of identical or similar products under a single work order. Each job has its own unique features. Under job costing work starts only after receiving the order from the customer. Normally it is of short duration.
The product is made as per the requirement of the customer. For example, there is a furniture shop where a customer says that he wants a 7-seater sofa and another customer says that he wants a 10-seater sofa. So, separate cost sheet will have to be prepared for a 7-seater sofa and a separate cost sheet will have to be prepared for a 10-seater sofa.
More examples of Job Costing: can be printing press, tailoring of dress, interior Decorators etc.
(b) Batch Costing:
This method of Batch costing is used in industries where the production is carried on in batches, it is a form of specific order costing, under which each batch is treated as a cost unit and costs are accumulated and ascertained separately for each batch.
Each batch consist of identical products which maintains its identity throughout one or more stages of production.
Each batch cost is used to determine the unit of cost of products. On completion of the batch the cost per unit can be calculated by dividing the ‘total batch cost’ by the number of units produced. This method of costing is suitable to industries where production consists of repetitive production in nature and specified number of products are produced in one batch.
Batch costing is done where identical products are being made in one lot, for example in pharmaceutical industry the medicines are being made in batches, the full lot of costing is known as batch casting and then it is divided into units, if the cost of the per unit has to be calculated.
More examples of Batch Costing: It is generally used in industries like engineering component industry, pharmaceuticals, footwear, bakery, readymade garments, toy manufacturing, bicycle parts etc.
(c) Contract costing:
This method of costing is defined as that form of specific order costing wherein work is carried out in accordance with the customer’s special requirement and is used in case of big jobs and therefore, the principles of job costing are applied to contract costing. The contract work usually involves heavy expenditure, spreads over a long period and is usually undertaken at different sites. Contracts are carried outside the factory, generally at the work site. Hence, each contract is treated as a separate unit for the purpose of cost ascertainment and control. Contract costing is also termed a terminal costing.
Job costing and contract costing are similar with only one difference that is job costing is for smaller duration while contract costing is for larger duration but products are made as per customers requirement.
For example, the contracts are generally of constructional nature like construction of roads, buildings, highways, bridges, water works, dams, etc. This method of costing is applied by builders, civil engineering contractors, ship builders etc. and various other mechanical engineering firms etc.
(ii) Operation Costing:
This method of Operating costing is used when goods are produced on mass scale and of the standardized nature without waiting for the order of the customer. The produced goods are kept in stock and the order of the customers are compiled from the stock of finished goods. The production takes place continuously. The production is of repetitive nature. As for example, cement, bricks, chocolates, clothes, paints, sugar etc.
This Costing includes the methods like:
(a) Process Costing
(b) Unit Costing
(c) Operating Costing
(d) Multiple Costing
(a) Process Costing:
This method of Process costing is used when the raw material has to pass through various processes, or stages before it is converted into finished goods and each process is distinct and well defined, the method employed for ascertaining the cost at each stage of production is called process costing. Even the production is continuous under this method.
In process costing the output of the first process becomes the raw material for second process and the output of the second process becomes the raw material for the third process and so on, until the product becomes finished goods ready for sale. The cost per unit at each process will be calculated by dividing the total cost by the number of units produced at each stage and the cost per unit of the final product is the average cost of all the processes.
For example: If you want to find the cost of product of its stage, then we do process costing where the product passes through various processes, from process P1 to process P2, process P2 to process P3 and so on each process cost is calculated separately. Separate accounts are created for each process.
This method may be applied in industries like – sugar, textile, bakeries, oil refining, food products, chemical, paper, paints, petroleum products etc.
(b) Unit Costing:
Unit Costing is a method of cost accounting where costs are determined per unit of a single product. It is known as “output” or “single output” costing. Unit costing is followed by the concern, which produces a single product on large scale continuously. The cost units are identical costs. Moreover, the products are having uniform homogeneous character. This method is suitable to industries where production is continuous and uniform and engaging in the production of a single product in two or three varieties.
The cost per unit is found by dividing the total cost by the total number of units produced. Unit costing is successfully followed in the production of homogeneous products.
For example: It is suitable for industries like collieries, quarries, brick works, flour mills, paper mills, cement manufacturing, pencil, pen, books, textile mills etc.
(c) Operating Costing:
Operating Costing is also called as Service Costing because this method is used in those undertakings which provide services or operating a service and are not engaging in manufacturing tangible products meaning costing is applied by those undertakings which provide services rather than the production of goods.
Total expenses regarding operation are divide by unit as may be appropriate.
For example, the total expenditure incurred by the bus company for providing service is divided by the total number of passenger kilometers.
Because of the varied nature of activities carried out by the service undertakings, the cost system used is different from that followed in manufacturing concerns. Industries which are suitable or applicable for operating costing are:
- Transport service: Bus, taxi, truck, railways, roadways, airways etc.
- Utility suppliers: Gas, Electricity, water supply
- Welfare services: Canteens, hospitals, libraries, hotels, nursing homes.
(d) Multiple Costing:
It is an application of more than one method of costing in respect of the same product meaning to know the cost of a product, several costing methods are used. Costs are to be ascertained for each component as well as for finished product. This involves use of different methods of costing for different components meaning multiple type of costing is done on every component and so it is known as ‘multiple’ or ‘composite’ costing.
For example: This method is suitable in industries where a number of components are manufactured separately and then assembled into a finished product. In cases of motor car, type writer, television, refrigerators, etc.
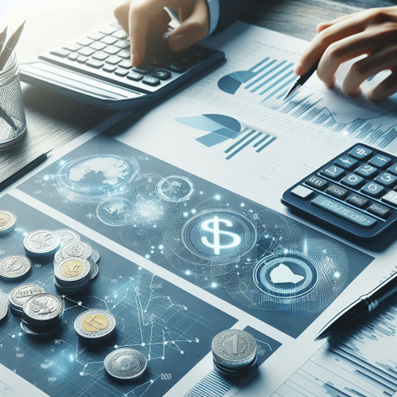
Summary of Methods of Costing
- Job Costing: For customized products made to order.
- Batch Costing: For products made in batches, like in a bakery or a pharmaceutical company.
- Contract Costing: For large projects like construction.
- Process Costing: For continuous production processes, like in a factory producing cement.
- Unit Costing: For single, standardized products made in large quantities.
- Operating Costing: For services, like transportation or utilities.
- Multiple Costing: Combining several methods for complex products, like cars or electronics.
Frequently asked questions
Why is costing important for businesses?
How do I know which costing method to use
Can costing methods change over time?
How does accurate costing benefit my business?
What tools can help with costing?
Is costing only about money?
Who should be responsible for costing in my business?
How often should costing be revised?
Conclusion of Methods of Costing
In summary, understanding and applying the right costing methods is crucial for businesses to effectively manage their production costs. These methods help companies figure out how much it costs to produce their goods or services, and they vary depending on the industry’s specific needs.
For custom or special orders, methods like Job Costing, Batch Costing, and Contract Costing are used. These focus on tracking costs for individual jobs, batches, or contracts, which are often unique or one-off projects. For mass-produced, standardized items, methods such as Process Costing, Unit Costing, Operating Costing and Multiple Costing are more appropriate. These help in calculating costs for continuous, large-scale production where products go through multiple stages or processes.
Choosing the right method allows businesses to keep their costs in check, price their products accurately, and ultimately run more efficiently. This can lead to better financial performance and a stronger position in the marketplace.